How to Manage GS1 QR Code For Food Recall
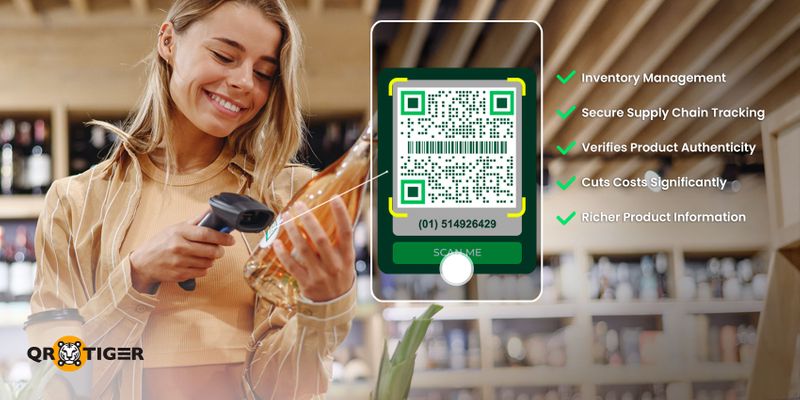
The GS1 QR code for food recall will transform how your business manages food recall. In the last five years, food recalls have risen across the globe. However, innovative businesses are finding smarter ways to handle these challenges.
Enter the GS1 QR code for recalls, and it's not just a smart solution; it's a game-changer for food safety. So, what's the big deal about these GS1 QR codes? They're like your food's digital ID card, packed with crucial information.
When customers scan the code, they can instantly access details about the product's origin, ingredients, and, most importantly, any recall notices. It means faster, more targeted recalls that can save lives and reduce food waste.
Implementing the GS1 QR code for food recall management is the best solution. You'll learn how to do that in this guide.
Table of Contents
- Why Should Your Business Prepare for Food Recalls?
- What Role Does the GS1 QR Code for Food Recall Play in Recall Management?
- 5 Steps to Include 2D Barcode in Your Food Recall System
- Step 1: Verify Which Elements Within Your SCM Will Benefit from GS1 Barcoding
- Step 2: Use a GS1 QR Code Generator to Create Compliant QR Codes
- Step 3: Implement GS1 2D Barcoding on Products and Shipping Information
- Step 4: Track Products and Batches with a GS1 QR Code for Food Recall
- Step 5: Link QR Codes to Other Aspects of Your SCM
- Create GS1 QR Code For Food Recall With Our GS1 QR Code Generator
Why Should Your Business Prepare for Food Recalls?
Wherever food recalls occur, their impact on the supply chain will be far-reaching. Therefore, companies within the supply chain should be ready to spring into action at a moment's notice. Your business should prioritize preparing for food recalls.
In the past, you may have had to manage a dozen recalls in a year; now, you might manage a dozen in a month. Depending on the size of your enterprise, you may manage a dozen recalls in a week.
Recent data on food recalls suggests this trend won't be slowing down. Instead, the data suggests there will be rapid growth in food recalls. When you understand what's causing the recalls, it's clear why more products are at risk.
Essentially, most food recalls occur because of three primary factors:
- Microbial contamination that affects both animal and plant-based products
- The presence of allergens in drinks and food.
- Mislabeling and labeling errors in products.
Because these reasons have their roots in the manufacturing process, there needs to be more supply chain businesses can do to prevent them. Instead, all SCM businesses can do is adapt to the rapid change. But, it's that rapid change that makes adapting challenging.
Being ill-prepared because of time constraints is not a worthy excuse for retailers, manufacturers, and legislators who expect you to carry out the food recall quickly and efficiently.
Therefore, it's imperative that you:
- Prioritize food recalls within your supply management processes
- Implement a straightforward solution to manage food recalls.
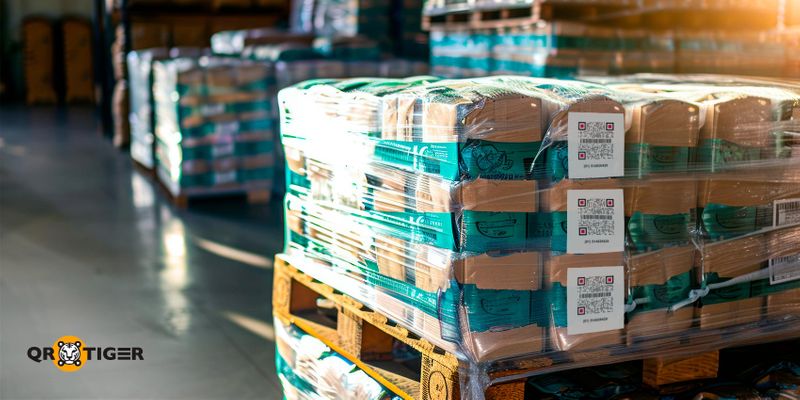
What Role Does the GS1 QR Code for Food Recall Play in Recall Management?
Food recalls will test the strength of your supply chain and the resiliency of the technology upholding it. A dynamic solution is necessary. Businesses may only discover that their processes and technology could be improved when they undergo a widespread food recall that tests their protocols and standards.
To understand how GS1 QR code for food recall benefits your enterprise, compare it to its predecessor: the 1D barcode.
- The 1D GS1 barcode has been the industry standard for years.
- One-dimensional barcodes relay linear data about the product, including quantity, content, and price.
GS1 barcode uses a charge-coupled device (CCD), so there isn't much room to innovate or update the data. Two-dimensional barcodes don't have this issue. A GS1 2D barcode relays far more data about the product.
These barcodes can contain static information like manufacturer, transit route, and expiration dates. Of course, it also transmits dynamic information, like whether the product is safe for consumption.
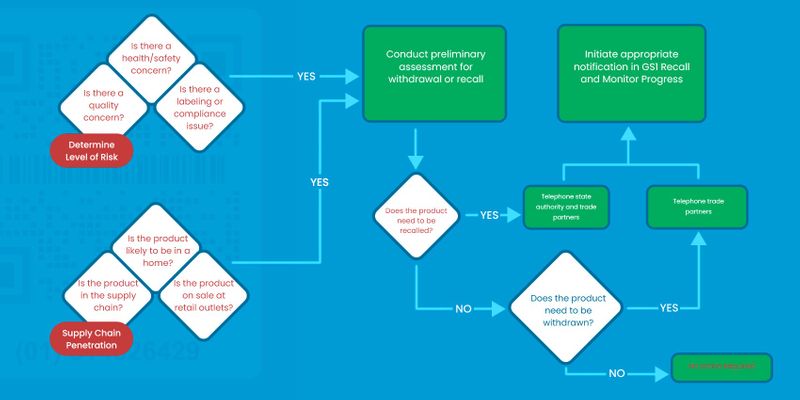
When you scan the 2D barcode of a product, you receive the most recent updates. Therefore, you know whether the products within your supply chain are currently undergoing a recall. It also means your company can act quickly based on changing data.
A GS1 barcode has three core benefits and quantifiable results: Improving traceability, increasing effective communication, and enhancing response time.
Improves Traceability
The best benefit of the GS1 QR code for food recall is its ability to improve traceability regardless of where a product is within the supply chain. In a global supply chain with many moving parts, every product should be traceable since any defect within this process could result in a recall.Listeria outbreak at multiple factories? The GS1 QR code will help you ascertain whether there is any effect on factories providing components within your supply chain. You can trace exactly where each part originates because of GS1 QR codes and then proactively create a plan should a brand or governing body initiate a recall.
There are dozens of real-world examples justifying why your business should leverage 2D barcodes, especially in a more complex supply chain.
Increases Effective Communication
When a food recall occurs, you want to be ready to share and receive information.Communication is pivotal in the recall process. A GS1 2D barcode allows you to maintain precise, up-to-the-minute data about products throughout the supply chain.
You can get the exact coordinates with QR codes for logistics of where the products are in the supply chain. Then, work to isolate those items to limit the negative impact on consumers.
Communicate Offline: Using GS1, you can communicate using links and static data. Therefore, you can still access and relay information whether or not you have internet access.
Relay an Extensive Amount of Data: There are no limits to how much data you can share using a GS1 QR code. You can add multiple GS1 links to these codes, using the same QR code to support partners in your supply chain and communicate with consumers.
Correct Errors When Necessary: Because these QR codes are GS1-compliant, you can edit the information in these GS1 links whenever necessary. When you do this, the information will update across channels and be available to all GS1-compliant scanners.
Enhances Response Time
Response time is paramount. The QR in QR code is an acronym for quick response, which is especially applicable in supply chain management when mere hours can have a significant impact.By accessing recall data using the GS1 QR code for logistics and supply chain, you can determine which products, including the brand and batch numbers, etc., are under recall.
You can then work to isolate the products, working with retailers in your supply chain to ensure they remove products from the shelf. You can also disable the barcode to guarantee the product won't scan at points of sale.
5 Steps to Include 2D Barcode in Your Food Recall System
Following are the five steps to include in your GS1 QR code for food recall:Step 1: Verify Which Elements Within Your SCM Will Benefit from GS1 Barcoding
As a company within the supply chain or logistics industry, your focus should be on where to place QR codes. You should include them on all shipments, even if suppliers don't provide them. Doing this allows you to control communication on all shipments and react quickly when a recall occurs.\When creating your GS1 links, use the correct GS1 digital link QR code barcode types. To track recalls, you want to create a "gs1:recallStatus" tag. Also, consider generating "gs1:masterData," "gs1:logisticsInfo," and "gs1:traceability" tags.
Step 2: Use a GS1 QR Code Generator to Create Compliant QR Codes
To ensure you use compliant QR codes, use a GS1 QR code generator that implements GS1 technology. A QR code generator that uses the GS1 standards will enable you to input, track, and trace all the relevant GS1 data. It also means your QR codes are scannable and valuable for businesses and partners in your supply chain.The world's leading brands have already made headway in implementing this technology that eliminates friction between suppliers. Your business should do the same to ensure your logistics and supply chain business remains relevant.
Step 3: Implement GS1 2D Barcoding on Products and Shipping Information
GS1 barcoding can help track and trace products. Therefore, consider adding it to shipping labels. Doing this will allow you to gain information about the product's journey regardless of where the product is in transit.This data could also help you track when a customer purchases a product from a retailer and how many items under recall a retailer sells.
Beyond that, the GS1 2D barcode can also inform consumers about purchasing an item under recall through the B2C GS1 link types.
Furthermore, it also means you can remotely remove the ability to scan a barcode under a recall from the point of sale -- whether self-checkout or at a cashier.
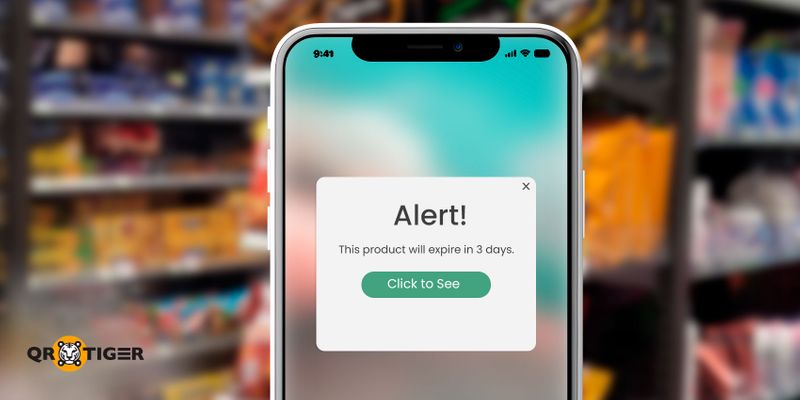
Step 4: Track Products and Batches with a GS1 QR Code for Food Recall
You need to know a product's location for effective recall management. Having location data ensures you know if a product reaches retailers, whether it's on the shelves, and if consumers are purchasing it.Remember, not every shipment and batch will reach shelves concurrently. Are some products still en route to retailers? The QR code can ensure your delivery staff doesn't offload those products under recall. If an item under recall reaches retailers, you can work to isolate these items.
You can disable the GS1 barcode to ensure that employees at retailers who scan the QR code before placing it on shelves know they must isolate the product. Using the GS1 QR code, you can also target specific batch numbers rather than entire product lines.
Step 5: Link QR Codes to Other Aspects of Your SCM
QR codes can be beneficial beyond food recalls and even help you be proactive. For example, you can trace where a shipment is coming from, when they manufacture these batches, and other pertinent information that could determine if a product recall is imminent.Over time, collecting this type of data can help you improve your supply chain and logistics. It also means you can make data-driven decisions.

Create GS1 QR Code For Food Recall With Our GS1 QR Code Generator
Food safety concerns are rising, and recalls have become an unfortunate reality in our modern food industry. But here's the good news: innovative businesses are finding smarter ways to handle these challenges. Enter the GS1 QR code for food recalls – it's not just a trendy tech solution; it's a game-changer for food safety.Adopting GS1 technology isn't just forward-thinking; it's becoming a necessity. As regulations tighten and consumer expectations rise, businesses that embrace this tech are positioning themselves as leaders in food safety and innovation. It's a win-win: better safety practices and a competitive edge in the market.
With QR TIGER, an advanced GS1 QR code generator, you can experience this incredible technology and include your business in the exciting shift to global collaboration.
DISCLAIMER: We acknowledge that GS1, as well as the materials, proprietary items, and all related patents, copyright, trademark, and other intellectual property (collectively, “intellectual property”) relating to its use, are the property of GS1 Global, and that our use of the same shall be in accordance with the conditions provided by GS1 Global.