How to Implement GS1 QR Code For Product Manufacturing
Maintaining the production process is crucial for any manufacturing business. With tight deadlines and high customer expectations, minimizing errors, tracking quality issues, and maximizing resource use are more important than ever. Digital technologies offer powerful tools to help manufacturers with these challenges. One solution is using GS1 QR codes to capture essential production data and share critical information across the supply chain.
This guide will explain how GS1 QR codes can improve your product manufacturing. We'll cover this barcode's basics, its inventory applications, quality control, scheduling, and more. Plus, we'll provide a step-by-step plan to help you get started. By the end, you'll see how adopting the GS1 QR code for product manufacturing can streamline operations, enhance visibility, and support business growth.
Table of Contents
What is a GS1 QR Code?
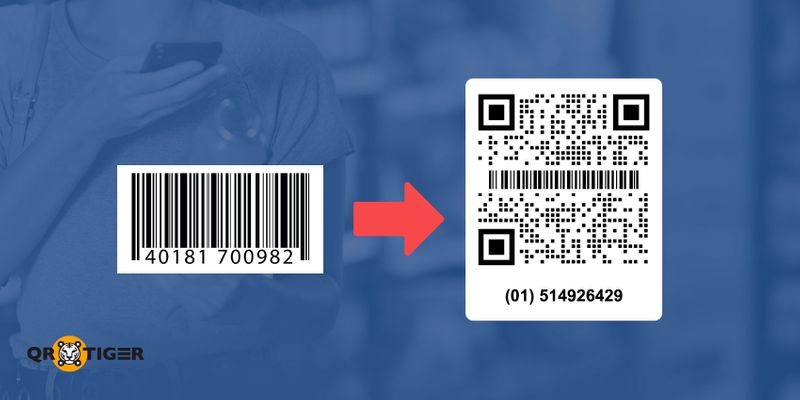
A GS1 QR code is a type of 2D barcode that holds detailed information, such as GTIN (Global Trade Item Number), batch numbers, expiration dates, and serial numbers. Unlike traditional barcodes with thin black lines, a QR code is a square filled with a grid of black dots, allowing it to store more data.
The "GS1" in the name means these QR codes follow international GS1 standards set by GS1, a global organization. This ensures that the data in the QR code is understood by systems worldwide, enabling smooth information sharing across the supply chain.
Creating and reading GS1 QR codes is straightforward. A smartphone with a GS1 barcode scanning app can scan the code and instantly display the encoded data, making it accessible without complex equipment.
Applying GS1 QR Code for product manufacturing
Now, let's look at how manufacturers can use GS1 QR codes at different stages of production:
Receiving and Inventory Management
Assign GS1 QR codes for manufacturing to all incoming raw materials and packages. During receiving, scan the codes to capture batch details, quantities, and expiration dates directly into inventory records. This automation speeds up data entry and provides real-time stock-level updates.
Work-in-Progress Tracking
Attach GS1 2D barcodes to products or containers at each workstation to record processing steps. Scanning the codes enables operators to track progress, while managers can monitor bottlenecks and inventory levels in real time.
Quality Inspection Of GS1 QR Code For product manufacturing
Embed pass/fail results from quality checkpoints such as material checks, equipment calibration, and final product testing into QR codes. It quickly identifies non-conforming items or batches with prior defects and helps pinpoint root causes for corrective actions."
Finished Goods Management
Label finished units and shipments with unique GS1 QR codes before warehouse transfer—scan codes during put-away and pick-and-pack to update stock records accurately. Shipment codes facilitate seamless receiving by customers and trading partners.
Production Scheduling
Use historical production cycle data from QR code scans to optimize resource allocation, balance workloads, and fine-tune schedules. This reduces lead times, rush jobs, and inventory carrying costs.
Customer Shipping
Embed GS1 QR code for product manufacturing on outbound shipments and packages. Customers can scan to access certificates of analysis and safety data sheets or return authorization information digitally, eliminating paperwork and enhancing customer experience.
Recall and Traceability
In a recall, trace affected batches and their distribution by scanning GS1 QR codes through the supply chain. This improves targeted communication, streamlines recalls and mitigates risks to reputation and sales.
5 Steps to Implement GS1 QR Codes in Your Facility
Successfully rolling out GS1 QR codes requires planning and execution. Here are the key steps to streamline implementation across your product manufacturing:
Adopt GS1 Standards
Register your company with GS1 to obtain GS1 Company Prefix codes for Global Trade Item Numbers (GTINs) and other identifiers. This establishes a foundation of standardized data that downstream customers and suppliers will understand.
Generate GS1 QR Codes
Use a reliable GS1 QR code generator to encode product, packaging and document information according to GS1 Application Identifiers. Integrate GTINs, codes, expiration dates, etc., for seamless data sharing.
Design Label Layouts
Develop barcode label templates specifying placements, graphics, disclaimers, and other elements according to your brand and regulatory standards. Test prints to validate scannability and peel-and-stick adhesion in manufacturing environments.
Configure Hardware and Software
Purchase barcode scanners, configure mobile devices, or set up fixed verifiers if needed. Integrate GS1 barcode tracking system scanning into your ERP/WMS to automatically capture and process information upon scans.
Implement and Train Users
Run pilots with selected products or processes before facility-wide rollout. Provide training materials, hands-on practice sessions and help desk support to onboard employees on the new procedures smoothly.
With proper planning, GS1 QR code adoption can be manageable. Start with high-impact areas and refine continuously to achieve optimal results over time.
Measuring Success and Driving Continuous Improvement
As a manufacturer, it is important to continuously monitor how well your GS1 QR code for the manufacturing program is working. Here are some suggestions for key metrics to track and ways to refine the program over time:
Track Inventory Accuracy Rates and Cycle Times
Measure inventory metrics such as stock-out rates, fulfillment accuracy, count variances, and receiving/put-away cycle times. Set monthly targets to reduce these metrics and improve processes. Lower inventory costs and fewer stockouts will save money.
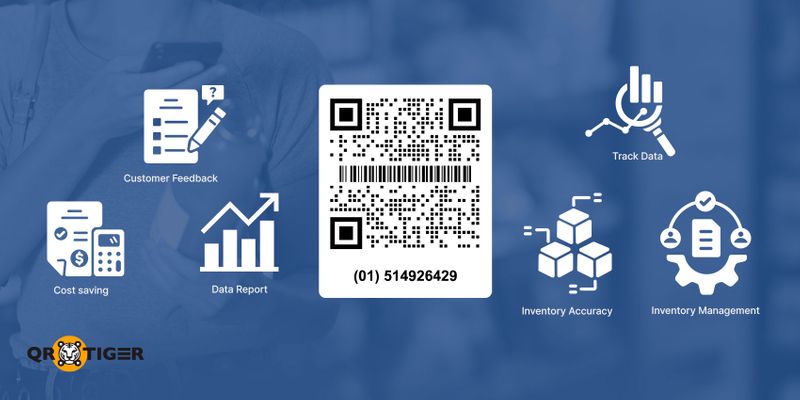
Analyze Production Metrics in Real-Time
Use GS1 QR code scan data to calculate performance indicators like equipment significance, machine uptime, wait times, and throughput rates. Identify bottlenecks and optimize workflows to speed up production and reduce costs.
Survey Staff for Feedback
Ask operators and supervisors how the new GS1 QR code for production services systems works. Send a quick online poll every few months. Pay attention to any pain points mentioned and solve problems fast. Happy workers do their jobs better and help systems improve over time.
Conduct Regular GS1 QR Code Compliance Audits
Double-check that all GS1 QR code for product manufacturing are correctly made with the special GS1 tools. There should be no typos or wrong info! Also, check that the equipment is calibrated correctly and that barcode labels stay scratch-free on items. Data errors waste time fixing things later.
Calculate Savings from Reduced Costs
At the end of each year, calculate the money saved from having less inventory carrying costs, throwing away fewer damaged goods, or recalls. Show senior managers the real dollar impacts as proof that the system works well. They will want to keep systems that make good savings!
Expand the Use of GS1 QR Codes Gradually
If GS1 QR code supply chain improves shipping, consider adding them to purchases, repairs, or training records. Gradual implementation minimizes disruption and helps employees adjust more easily.
Drive Continuous Improvement Culture
Create a team to review metrics and surveys regularly. Continuously brainstorm and adjust processes as technology evolves to maintain and enhance benefits. Monitoring and refinement ensure sustained ROI and success with 2D barcodes.
Embrace Future-Ready Production with GS1 QR Codes
Implementing the GS1 QR code for product manufacturing can transform how you manage and track operations. These versatile codes enhance inventory management, quality control, and traceability by providing detailed, real-time data. From streamlining receiving and inventory management to improving work-in-progress tracking and final product inspection, GS1 QR codes offer a comprehensive solution for modern manufacturing challenges.
You can integrate these codes smoothly into your operations by following a structured implementation plan—adopting GS1 standards, generating QR codes, designing labels, and training staff. Regular monitoring and adjustments based on critical metrics and feedback will help maintain and improve the benefits.
Embracing GS1 QR codes reduces costs and errors and positions your business for future growth. Start implementing today to streamline your processes and enhance overall efficiency. Visit our website to create a GS1 QR code for product manufacturing.
DISCLAIMER: We acknowledge that GS1, as well as the materials, proprietary items, and all related patents, copyright, trademark, and other intellectual property (collectively, “intellectual property”) relating to its use, are the property of GS1 Global, and that our use of the same shall be in accordance with the conditions provided by GS1 Global.